WELCOME
About Us
The office address of Shenyang Great Wall Gear Factory (Shenyang Changcheng Gear Manufacturing Co., Ltd.) is located in the northeast big city, known as "the birthplace of one dynasty, the capital of two generations of emperors"-Shenyang, No. 362 Tianshan Road, Huanggu District, Shenyang City, was registered in the Market Supervision Administration of Huanggu District, Shenyang City on August 1, 1988. The new account is registered at 10 million RMB. In the 37 years of the factory's development and growth, we always provide customers with good products and technical support, sound after-sales service, our factory mainly engaged in gear manufacturing, mechanical parts processing, the main spiral bevel gear (arc gear).
Why choose us
The production of spiral bevel gear (arc gear), by the majority of customers love.
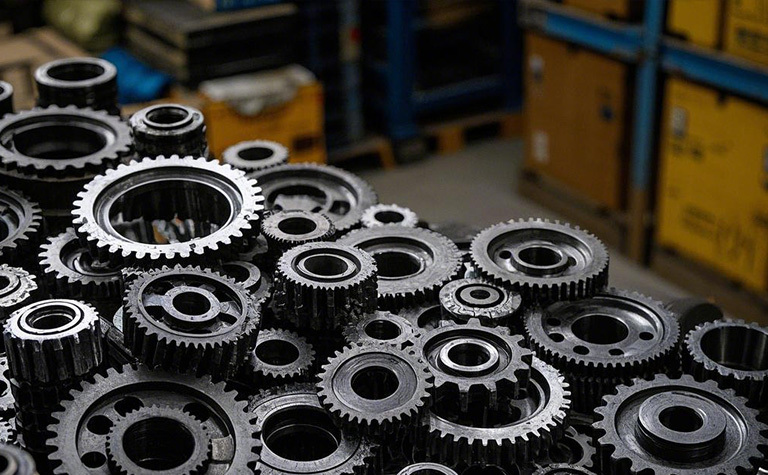
We are the factory
We are a source of strong strength manufacturers, with their own production base and team, to achieve direct supply of products.
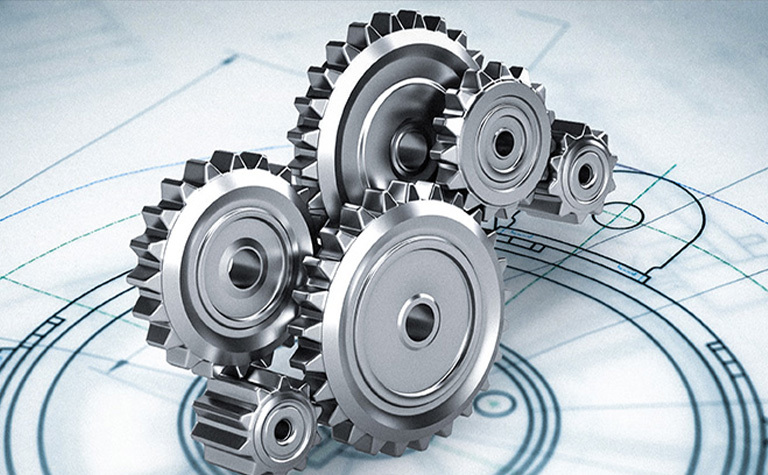
We can customize
We know that each customer's needs are different, so we focus on on-demand production customization, from design conception to finished product delivery, each link is closely around your unique requirements.
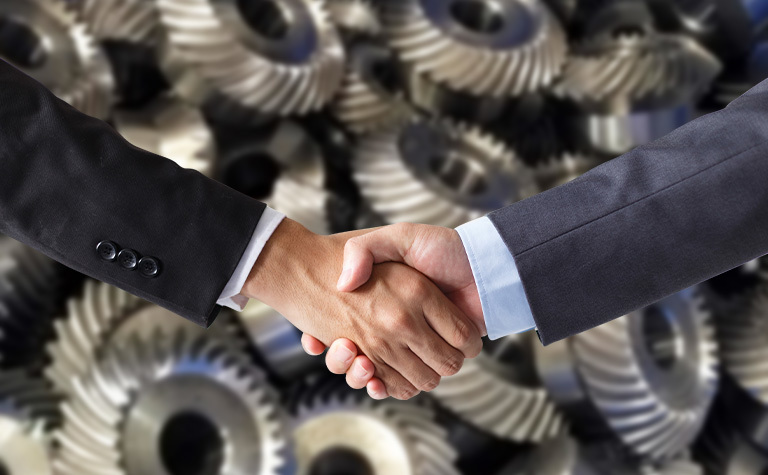
Perfect after-sales
Perfect logistics after-sales service, from transportation to delivery of the whole protection, so that you have no worries, rest assured to buy.
recommend Products

Mining Industry
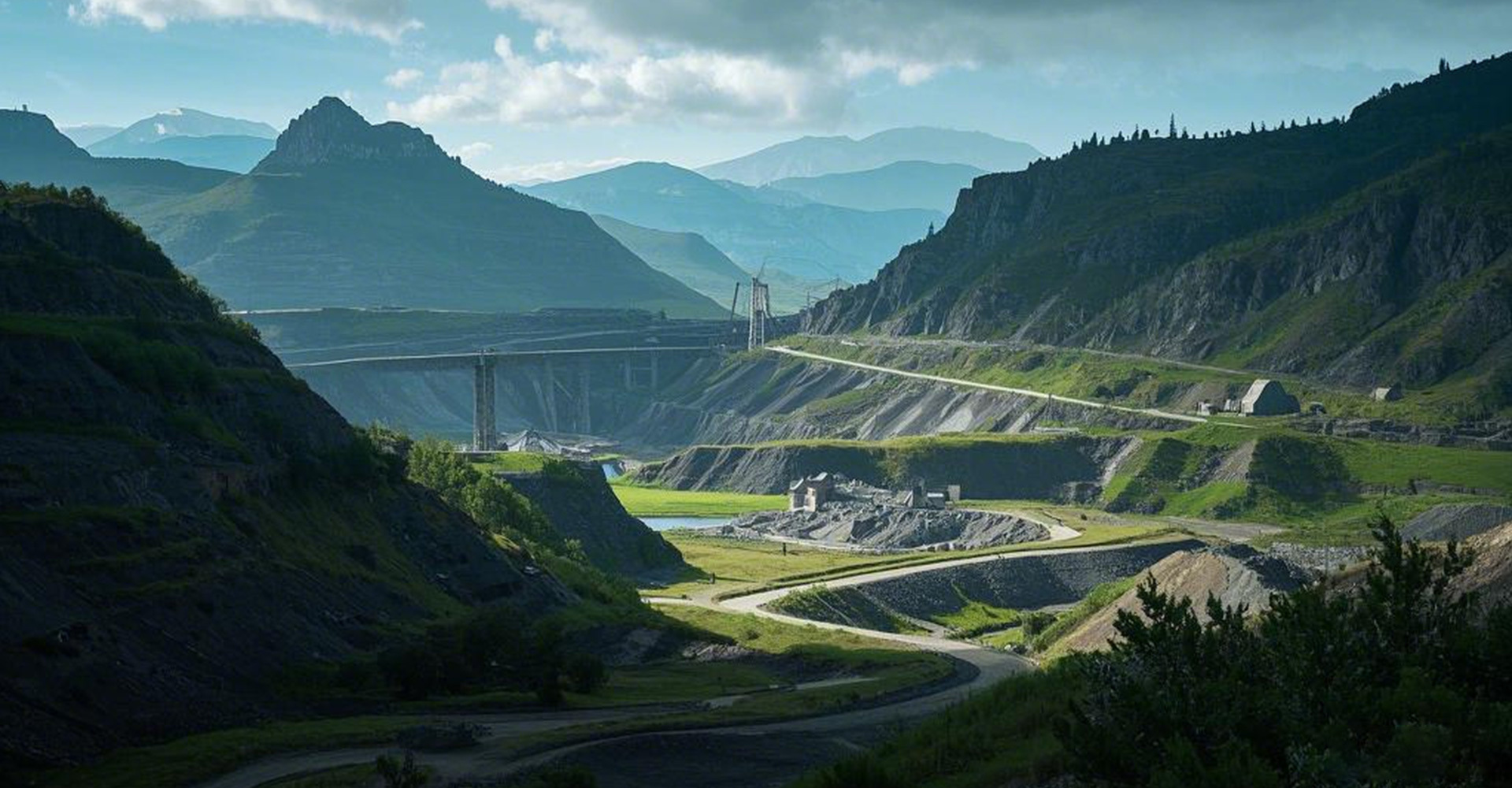

Power station industry
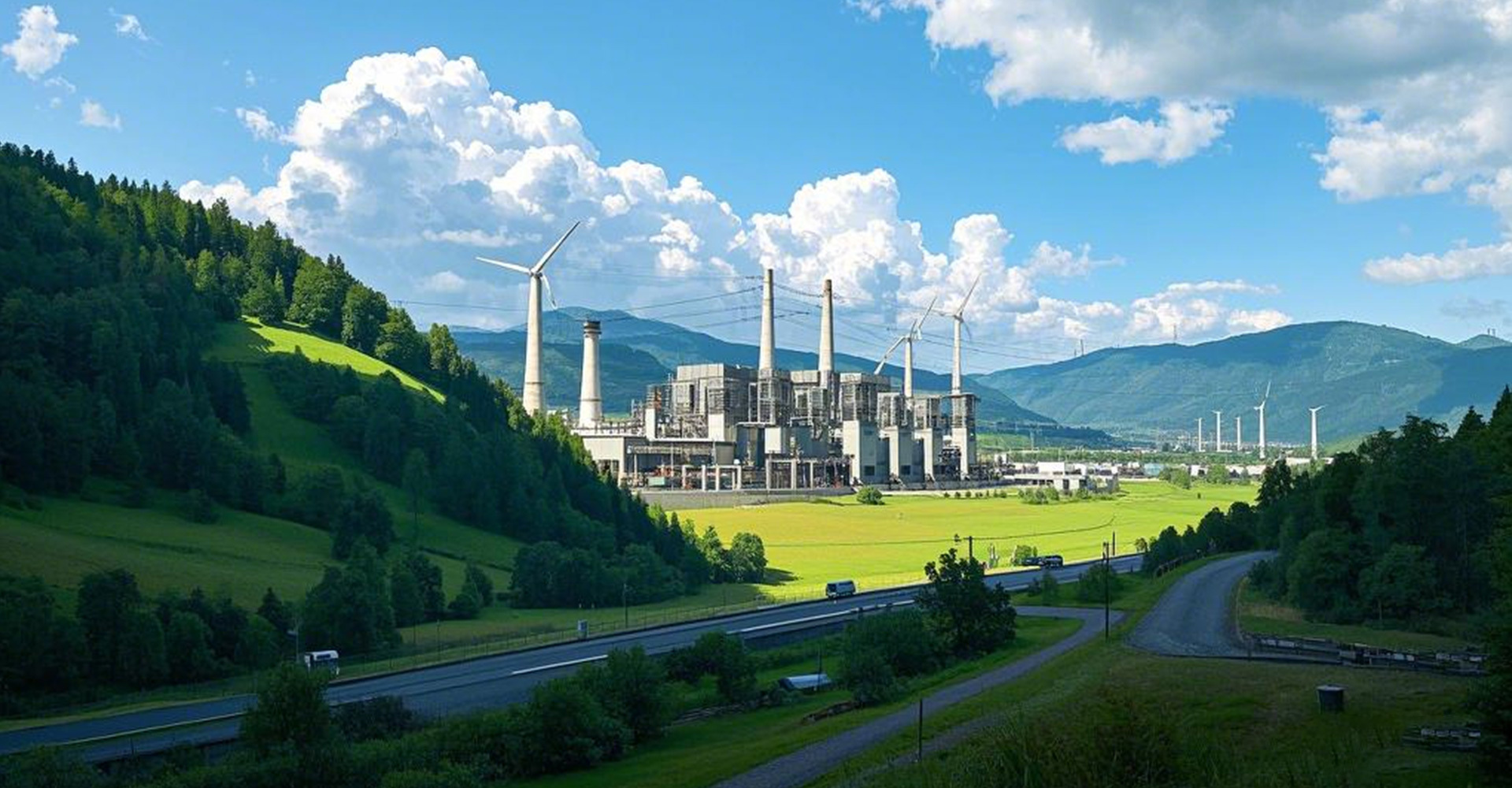

Chemical industry
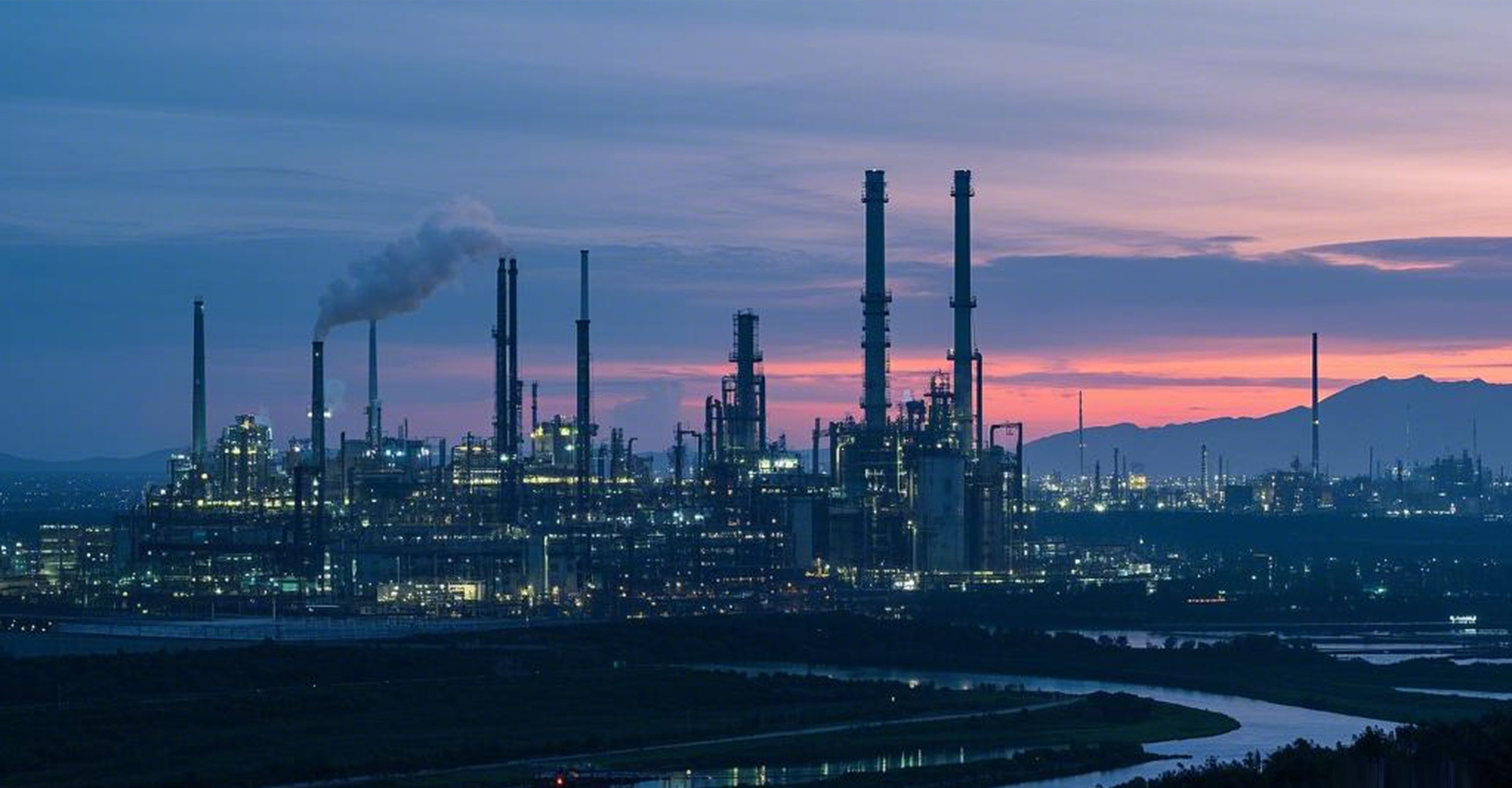

Coal mine equipment
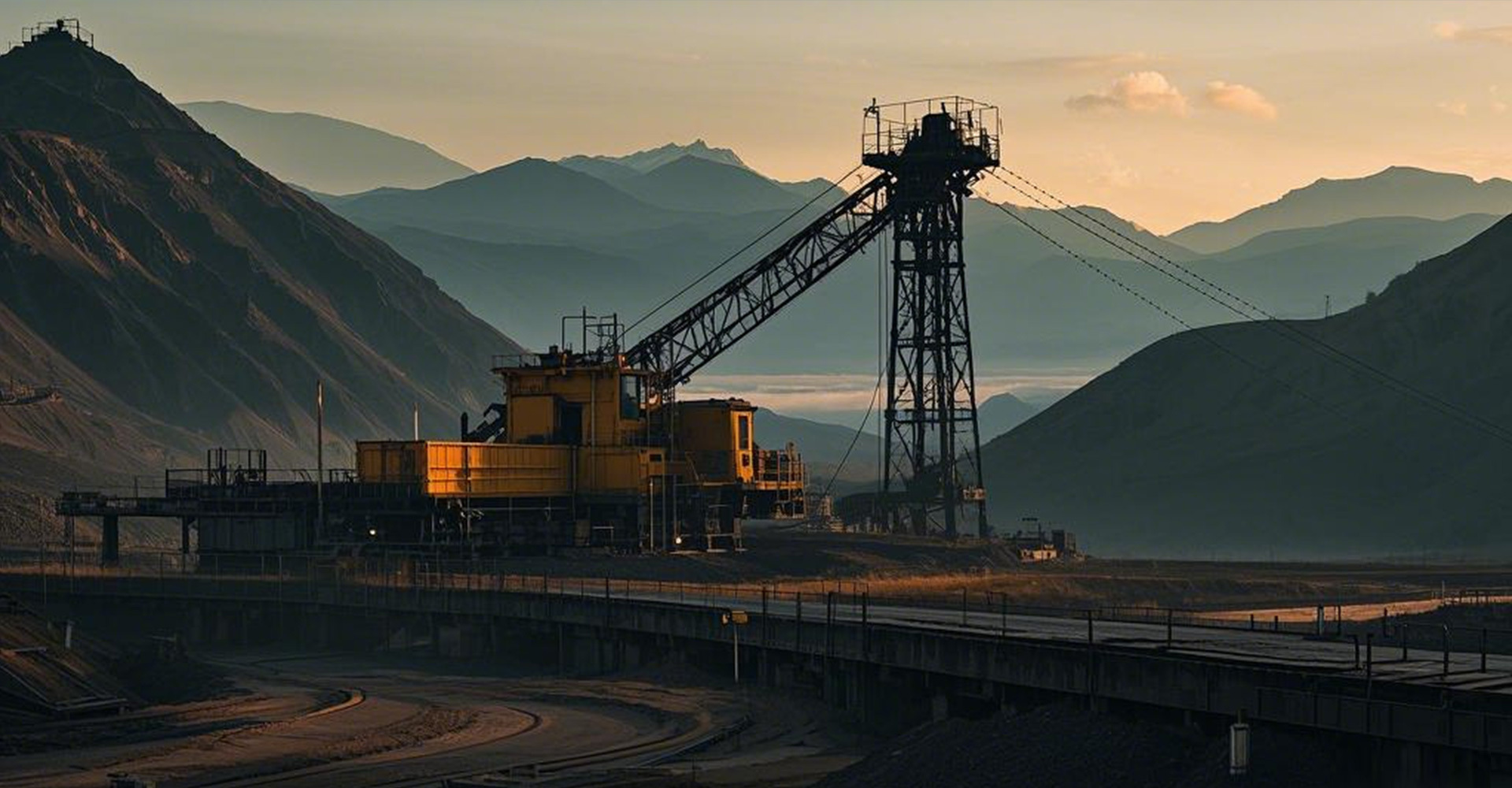

Thermal power generation
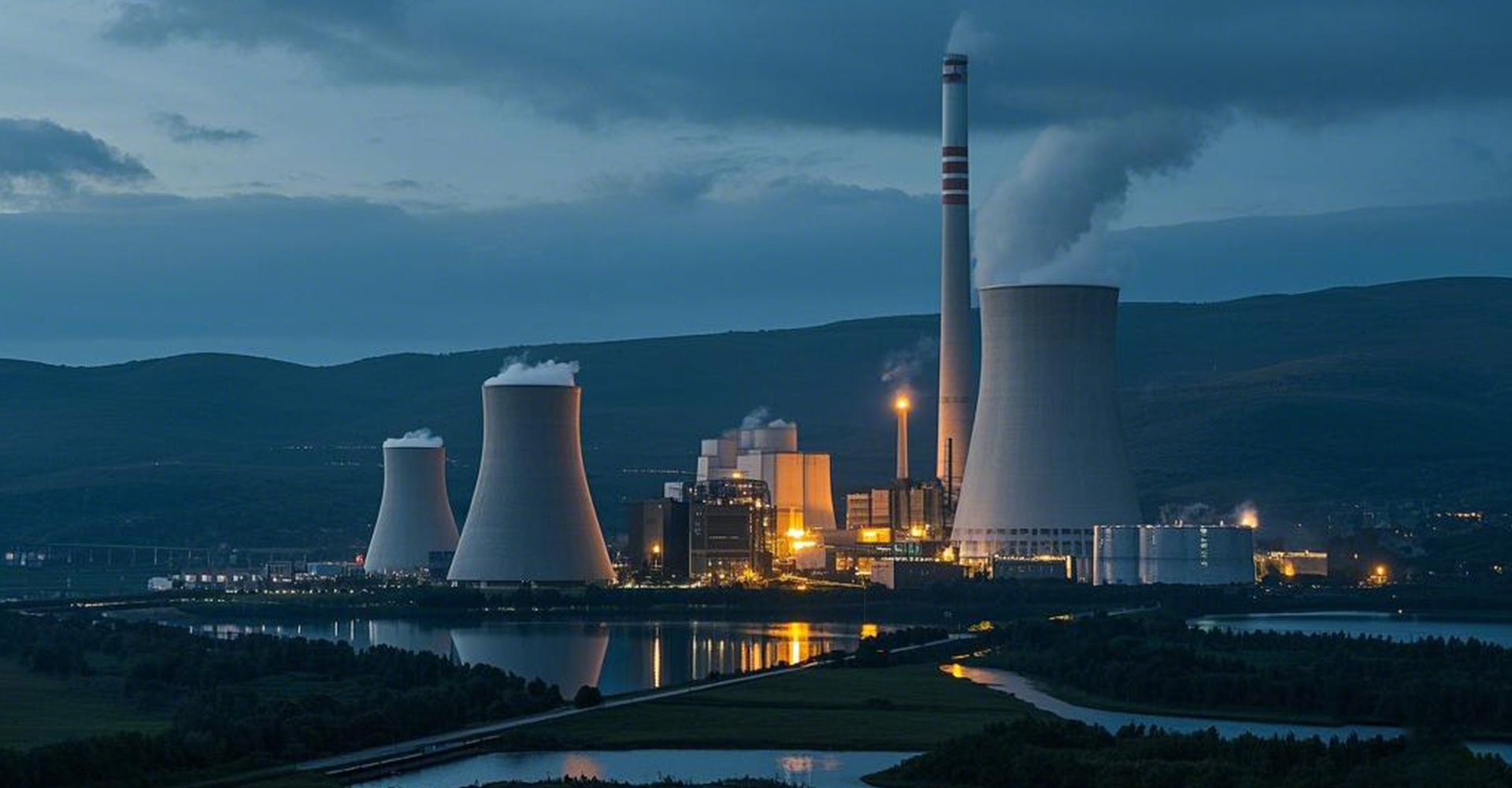
Application
Application areas
Widely used in domestic and foreign oil field petrochemical machinery, all kinds of machine tools, all kinds of mechanical processing equipment, engineering machinery, metallurgical equipment, steel rolling machinery, mining machinery, coal mining machinery, textile machinery, marine machinery, shipbuilding industry, aerospace, forklift, elevator, reducer, aircraft manufacturing, etc.
Blog
Introduction to Gear Processing Methods and Selection
2023/07/25
Gear processing is very widespread in industrial production and is one of the important components for transmitting motion and power. The operational function, load capacity, service life, and operational precision of the product are all closely related to the quality of the gear itself. Therefore, the methods and choices for gear processing are very important. With the development of production technology, the requirements for the operational precision of mechanical products are becoming increasingly high, as well as the demands for power transmission and speed. In the gear processing production process, the control of fine deformation and process stability is relatively complex. After the blank is cast, isothermal annealing needs to be selected to achieve good processing functionality and a trend of uniform metallographic arrangement deformation; cylindrical gears can be processed using two methods: honing and grinding. Grinding has a lower cost, but the correction of the tooth shape is relatively weak. Requirements for gear processing: 1. Accuracy of motion transmission: To improve the precision of the equipment, the accuracy of motion transmission is very important for gears as key components. 2. Stability of transmission: To reduce processing losses in equipment, the stability of gear transmission must be improved. This requires changing the transmission ratio at the moment of scale transmission to avoid impacts, vibrations, and noise, which could even lead to gear failure. 3. Uniformity of load distribution: This is to prevent the lifespan of the gear from being affected by local wear on the tooth surface. It is required that the tooth surface has good contact with the gear during meshing to prevent stress concentration. 4. Transmission clearance: To provide space for storing lubricating oil, it is required that there is a certain gap between the gear and the non-working tooth surface during meshing. Currently, gear processing mainly uses cutting methods, but casting or rolling methods can also be employed. Casting has low precision and high surface roughness, while rolling has high productivity and good mechanical properties but still has low precision and is widely used. This article is sourced from the internet. If there are any issues, please contact us!
View moreGear Processing Technology Process (7 Steps to Make It Simple)
2023/06/22
Methods of gear processing include the forming method, which uses a forming milling cutter that matches the shape of the tooth slots exactly to cut the tooth profile, such as gear milling; and the generating method, which uses the mutual meshing motion of the tool and the passive gear to cut the tooth profile, such as gear hobbing and gear shaping. Let's take a closer look at the gear processing technology flow. Gear Processing Technology Flow 1. Forging Blank Hot die forging is still a widely used blank forging process for automotive gear components. In recent years, wedge rolling technology has been widely promoted in shaft processing. This technology is particularly suitable for producing blanks for relatively complex stepped shafts, as it not only has high precision and small machining allowance for subsequent processing but also has high production efficiency. 2. Normalizing The purpose of this process is to obtain a hardness suitable for subsequent gear cutting processing and to prepare the structure for final heat treatment, effectively reducing heat treatment deformation. The gear steel material used is usually 20CrMnTi. Normalizing is greatly affected by personnel, equipment, and environment, making it difficult to control the cooling rate and uniformity of the workpiece, resulting in large hardness dispersion and uneven metallographic structure, which directly affects metal cutting processing and final heat treatment, leading to large and irregular thermal deformation, making it impossible to control the quality of the parts. Therefore, isothermal normalizing technology is adopted. Practice has proven that isothermal normalizing effectively changes the disadvantages of general normalizing, resulting in stable and reliable product quality. 3. Turning Processing To meet the positioning requirements for high-precision gear processing, all gear blank processing is done using CNC lathes, employing mechanical clamping without regrinding the cutting tool, achieving synchronous completion of hole diameter, end face, and outer diameter processing in one clamping. This ensures the perpendicularity requirements between the inner hole and the end face, while also ensuring small size dispersion in large batch production of gear blanks. This improves the precision of the gear blanks and ensures the processing quality of subsequent gears. Additionally, the high efficiency of CNC lathe processing significantly reduces the number of equipment needed, making it economically favorable. 4. Hobbing and Shaping The equipment used for processing the teeth still largely employs ordinary hobbing machines and shaping machines. Although they are easy to adjust and maintain, their production efficiency is relatively low, and if large production capacity is required, multiple machines need to operate simultaneously. With the development of coating technology, it has become very convenient to re-coat hobs and shaper tools after grinding. Coated tools can significantly improve service life, generally increasing it by over 90%, effectively reducing the frequency of tool changes and grinding time, resulting in significant benefits. 5. Skiving Radial skiving technology is widely used in large-scale automotive gear production due to its high efficiency and ease of achieving design requirements for tooth shape and orientation. Since the company purchased specialized radial skiving machines from an Italian company in 1995, this technology has been applied maturely, with stable and reliable processing quality. 6. Heat Treatment Automotive gears require carburizing and quenching to ensure good mechanical properties. For products that do not undergo further grinding after heat treatment, stable and reliable heat treatment equipment is essential. The company has introduced a continuous carburizing and quenching production line from Germany's Linde Company, achieving satisfactory heat treatment results. 7. Grinding Processing This mainly involves precision machining of the inner hole, end face, and outer diameter of the gear after heat treatment to improve dimensional accuracy and reduce geometric tolerances. Source: Internet. If there are any issues, please contact us!
View moreWhat details should be paid attention to during gear processing?
2023/05/16
Gear processing is an important direction in mechanical processing, with a very wide range of applications, such as in automobiles, airplanes, machine tools, and port lifting equipment, among others. There are many methods for gear processing, the main ones being milling, rolling, grinding, turning, and filing. However, different processing methods are suitable for different types of gears and processing situations. During the gear processing process, there are many details to pay attention to, and below, the gear processing manufacturer will introduce some of them. 1. Reasonable Matching of Processing Tools The reasonable matching of processing tools is a very critical link in the gear processing process. When selecting cutting tools or grinding tools, one should comprehensively consider the material, shape, and precision requirements of the gear. For gears produced in large quantities, it is advisable to use multi-tooth turning tools to improve productivity; for samples or small batch production of gears, special processing tools with low cutting force, high processing precision, and long service life should be selected. 2. Selecting Appropriate Processing Parameters and Methods In gear processing, the selection of processing parameters and methods directly affects processing precision and the surface quality of the workpiece. Therefore, it is necessary to reasonably select processing parameters such as cutting speed, feed speed, cutting depth, and cutting width according to the requirements of different gears, and to fully consider possible defects such as thermal deformation, burrs, and cracks that may occur during processing. 3. Strictly Control Processing Errors Processing errors are one of the key factors affecting the quality of gear processing. They include shape errors, measurement errors, and clamping errors, so it is essential to strictly control these errors during the gear processing process. When selecting processing equipment, it is advisable to choose machine tools with stable performance, high automation levels, high precision control systems, and reliable detection equipment; during operation, one should strictly follow the standard operating procedures and strive to avoid errors caused by operational mistakes. 4. Pay Attention to Lubrication and Heat Dissipation Lubrication and heat dissipation are very important during the gear processing process. Appropriate lubrication methods can reduce tool wear, decrease friction, and prevent burrs and thermal deformation; reasonable heat dissipation methods can lower processing temperatures, shorten processing times, and improve processing efficiency. When selecting lubrication and heat dissipation methods, one should consider factors such as processing type, materials, and environment comprehensively. 5. Strengthen Maintenance and Care Strengthening the maintenance and care of old machine tools can not only improve the service life and processing precision of the machine tools but also reduce mechanical failures and downtime for repairs, thereby enhancing the production efficiency and economic benefits of the gear production line. For new machine tools, they must be used according to installation, debugging, and usage regulations, and strict maintenance work such as cleaning and replacing consumable parts should be carried out. 6. Strengthen Inspection and Control During the gear processing process, it is necessary to correct and control the errors generated during processing, and to strengthen quality inspection and control, which can reduce processing errors and improve production quality. Especially in high-precision gear processing, large and high-precision coordinate measuring machines have become indispensable tools. After processing is completed, gears should also undergo inspection work such as tapping, four-point measurement, and vibration detection, with timely adjustments made upon discovering issues. The content of this article is sourced from the internet. If there are any issues, please contact me for deletion!
View moreTechniques for Rust Prevention in Gear Processing: How to Extend the Lifespan of Gears?
2023/04/03
Gears, as important components of mechanical transmission, often operate in environments with high temperatures, high pressures, high speeds, and heavy loads. To ensure the lifespan and reliability of gears, rust prevention treatment is necessary. This article summarizes the following suggestions based on research into rust prevention techniques for gear processing, to help readers better protect gears and extend their service life. 1. Choose Suitable Materials The choice of material for gears has a decisive impact on rust prevention treatment. Common gear materials on the market include steel, copper, cast iron, and aluminum alloys. Steel is a commonly used material for manufacturing gears, known for its high strength and good fatigue resistance, but it is also prone to rust. Therefore, when choosing steel as the gear material, it is important to consider using appropriate rust-proof coatings for corrosion protection. Copper and cast iron materials generally have better corrosion resistance compared to steel, so they usually do not require rust prevention treatment. Additionally, aluminum alloy gears do not need extra rust prevention treatment due to their inherent rust resistance. 2. Perform Surface Treatment The surface of the gear is easily damaged during operation. Therefore, appropriate surface treatment during processing can not only improve the surface quality of the gear but also enhance its corrosion resistance. Common surface treatment methods include chrome plating, electro-galvanizing, hot-dip galvanizing, and phosphating. 3. Use Appropriate Rust-Proof Coatings Rust-proof coatings are an effective means to enhance the rust and corrosion resistance of gears. Currently, widely used types of rust-proof coatings on the market include organic coatings, inorganic coatings, and coating composites. Among these, inorganic coatings are the most widely used because they can effectively prevent rust without damaging the performance of the gear itself. 4. Properly Control the Working Environment When using gears, it is advisable to avoid exposing them to high temperatures, high humidity, dusty, and corrosive gas environments, as these can accelerate rusting. Some common working environment impacts on gears are as follows: (1) High-temperature environment: This can lead to oxidation of the gear surface, reduced hardness, and accelerated wear of the tooth surface, so it is best to avoid excessive temperatures when using gears. (2) Humid environment: This can cause moisture to accumulate on the gear surface, and in a file bag environment, it can lead to rusting of the gear surface, so it is important to ensure that the storage environment for gears is dry. (3) Dusty environment: Dust can enter the interior of the gear, damaging the surface and tooth surface, so the time gears spend working in dusty environments should be minimized. (4) Corrosive gas environment: Environments with acid mist, alkaline mist, etc., can corrode the surface and tooth surface of the gear, causing damage. 5. Conduct Regular Inspections During use, gears will inevitably encounter some issues. Therefore, regularly checking the wear condition of the gears and repairing them in a timely manner can effectively extend their service life. Regular inspections of gears mainly include the following aspects: (1) The condition of corrosion and rust on the gear surface; (2) The wear condition of the gear teeth; (3) The quantity and quality of the gear lubrication oil; (4) The coordination of gear transmission: Good coordination among the gears in transmission is essential; otherwise, it can lead to increased wear of the tooth surfaces. The content of this article is sourced from the internet. If there are any issues, please contact me for removal!
View more